

They first started off with drawing a Cause and Effect diagram. A core team was formed and they started to work on the problem. The Quality team was called and asked to solve the problem. It is a very good tool for root cause analysis and a part of 7 Basic Quality Control Tools. The bank’s management wants to understand the reasons for the high queue and reduce the queue so that it can serve more number of customers and also reduce the waiting time of its customers. One of the branches located in the main part of the city has high a very high queue to manage during most of its operating time. Assume a famous bank, having branches in few parts of the city. Branch out for necessary sub causes under the main causes, if necessary.List down all the identified causes into any of the six categories.Brainstorm all the possible causes and sub causes that impact the problem.Write the Six main categories on the board.Team up all the relevant members who are knowledgeable in the problem under study.Identify the problem area and define the problem clearly.Thus, the entire company must seek to know what are the 7 basic tools of quality and how they can benefit the functioning of the organization's processes. The use of quality tools, such as the Ishikawa diagram, also known as Fishbone Diagram, is essential to maintain good management, products / services within specifications and meet customer expectations.

User can branch out sub causes till the level he feels that is relevant to the problem. This guide helps you to learn about what is the Ishikawa Diagram, the 6 M's of production and the steps to create your own Diagram. Al the potential causes that might impact the problem are listed under these main causes. It has six main branches: Men, Material, Method, Machine, Measurement, and Mother Nature. Fishbone diagram looks like the skeleton of a fish. It is also considered as one of the Seven Tools of Quality. He first listed down all potential design features to be available in a product under different headers. It is also called a “ Cause and Effect” diagram, because it lists down all the potential causes for a given effect.Īs the name indicates, this tool was developed by Prof. Other than that, Ishikawa diagram is also used in New Product Development for identifying all the potential features. Thus it is one of the important tools used for problem solving methods like DMAIC, PDCA, and many other projects. The purpose of this tool is to list down ALL the potential root causes leading to a problem. It includes the raw information coming in, on through the final output that is delivered to the customer.Ishikawa Diagram otherwise known as Fishbone diagram is one of the tools most commonly used by Quality Professionals.
#Ishikawa diagram in six sigma software#
It may include corporate wide systems, or individual software packages installed on a computer. Program: Program, in this usage, refers to software programs.Plant: The physical layout of the building and the proximity to other locations fall into this category. Ishikawa Diagram otherwise known as Fishbone diagram is one of the tools most commonly used by Quality Professionals.Be careful not to assign process, policy, or program causes to people.
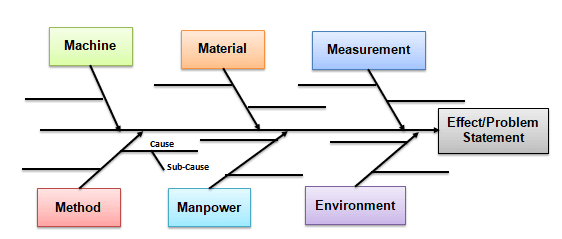
People: The makeup, size, and skills of a team all have an impact on the effect you are looking at in your fishbone diagram.Informal processes are sometimes called the “hidden factory”, or the “hidden office.” Process: Processes may be formal or informal.The degree of flexibility in responses to customers, for example, is often guided by policy-driven rules. Policy: Policy affects office environments much more than they affect the shop floor.
